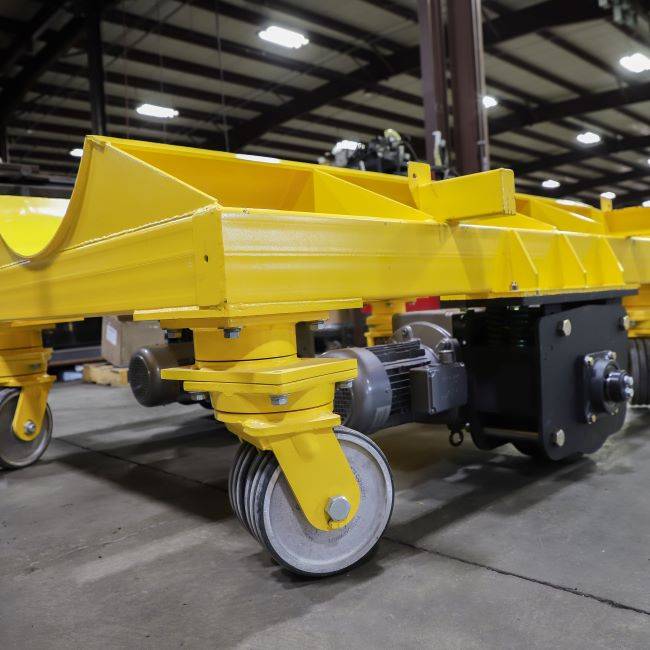
Crushing It: Motorized Flaker Cart Efficiently Moves 16,000 lb. Rollers In Spark-Free Facility.
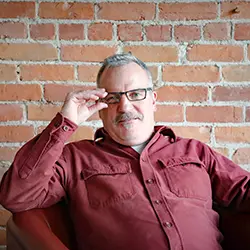
Conceptual Innovations designs non-sparking motorized carts to carry flaking rollers with a high degree of accuracy and movement.
Situation
A raw agricultural commodities trader contacted Conceptual Innovations regarding upgrading their flaker cart fleet. A flaker cart is a type of mobile equipment used in the food industry, specifically in the production of flaked grains. It is typically used to crush oilseeds such as soybeans, canola, and sunflowers into flakes, which can be collected in a hopper or bag for transport or further processing.
Flaker carts need to be mobile, as they’re moved to different locations to collect the flakes and for periodic maintenance on the rollers used in processing. This was where some new challenges came to light. Up to this point, the company relied on overhead cranes to move the 16,000-pound rollers onto a cart, which a tugger then moved. This also required employees stationed at the corners to help steer the cart.
Now that the company has just moved into their new facility. They quickly found that there wasn’t enough room for equipment and people to move the rollers.
And the challenges didn’t end there. Besides the logistical problems they faced, one of the most critical challenges was working inside a grain processing facility. The grain dust generated during processing is highly flammable. A volatile situation requires any transportation vessel to move the grain to avoid any chance of spark or flame.
Solution
That is when they reached out to Conceptual Innovations. To solve the non-sparking requirements, Conceptual Innovations designed and fabricated a cart to carry the flaking roller in a cradle fashion. Powering the cart required two DRIVE CASTER® consisting of five-horsepower, explosion-proof 480 Volt AC motors and an energy-efficient right-angle gearbox.
Conceptual Innovations also utilized Caster Concepts, a premier Caster Company Specializing in Heavy Duty Casters. These casters were especially suited for this application, consisting of 97 Series Casters with dual swivel sections. These casters allowed an excellent range of movement, thus reducing wheel scrub and less caster binding during direction changes under load.
This system was topped off with a user interface that allowed the operator to control each drive independently, allowing a high degree of control and accuracy when positioning the cart for loading and unloading operations.
Other features of the DRIVE CASTER® solution include:
- High-quality and wear-free helical and bevel gearing
- Robust UNICASE cast iron housing
- High-quality helical gearing up to AGMA Class 13
- High-performance inverter/vector duty motors and brake motors
- Protective features for severe duty and washdown environments
- Oil-safe QUADRALIP seal system
- AUTO VENT breather regulates internal pressure and keeps contaminants out
- Stainless steel (316) protective paint coating – USDA/HI compliant
The system was topped off with a user interface that allowed the operator to control each drive independently, allowing a high degree of control and accuracy when positioning the cart for loading and unloading operations.
Results
The customer could move the casters quickly on their concrete decking. The speed/power of the cart allowed the operators to achieve a high degree of accuracy and safety in a dangerous environment. It also eliminates the need to install additional overhead cranes and multiple people tuggers manhandling a 16,000 lb. load in a space-constrained area.